Die Basis für den Sandguss bildet immer ein Modell des zu gießenden Teils. Dieses Modell wird in der Regel von einem Modellschreiner aus Holz, Kunstoff oder selten sogar aus Guss hergestellt und die Oberfläche bei Holz zur Vergütung und zum Schutz vor Verzug durch Feuchtigkeit gespachtelt und lackiert. Positiver Nebeneffekt ist, dass die geschlossene Oberfläche gut abformbar ist und keinen Einfluss auf den Feuchtigkeitsgehalt des Formsandes hat.
Wichtig beim Guss ist generell die Tatsache, dass das Gussmaterial mit der Abkühlung schrumpft, also schwindet. Das Modell muss also vorher entsprechend berechnet werden und je nach Form und Legierung um knapp 2 % größer als das gewünschte Teil sein.
Die Firma ist eine der wenigen Gießereien, welche fast ausschließlich Sandguss mit Natursand betreibt, der sich hauptsächlich aus einem sehr feinen Sand und Ton als Bindemittel zusammensetzt. Für haltebare und problemlos gießbare Formen ist der Feuchtigkeitsgehalt des Sandes entscheidend. Deswegen prüft der Handformer laufend die Sandqualität und gibt bei Bedarf vorsichtig Wasser hinzu. Das wahre Können der Gießerei wird vor allem bei komplexen Gussteilen mit Hinterschneidungen, Ausformung mit Ausballungen, mehreren Modellteilen mit Aufstampfklötzen und vielen Kernen deutlich, zur Beobachtung des Form- und Gussvorgangs und zur anschaulichen Dokumentation wurde hier aber bewusst eine einfache Kontaktscheibe gewählt.
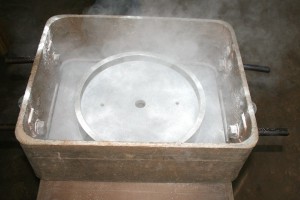
Zunächst wird der Unterkasten aus Sicht des späteren Gussvorgangs falschherum auf einem ebenen Tisch platziert und das Modell so eingelegt, das ringsherum ein möglichst gleicher und genügender Abstand zum Rand des Unterkastens gegeben ist. Das Modell und der Tisch werden anschließend mit Talkum bepudert, um später eine leichte Entnahme aus dem Sand sicherzustellen. Bei Modellen mit tiefen Aussparungen kommt auch Graphit als Trennmittel zum Einsatz.
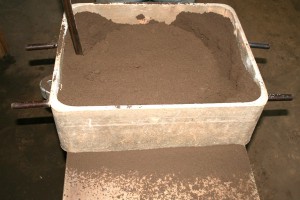
Im nächsten Schritt wird Naturformsand in den Kasten gesiebt und in mehreren Schritten verdichtet. Hierzu verwendet man bei kleinen Modellen vor allem die Hände und Stampfwerkzeuge (zunächst kleine Spitzstampfer für einen guten Anpressdruck an den Konturen und später gröbere Plattstampfer für die vollflächige Verdichtung), bei sehr großen Kästen werden auch pneumatische Stampfer verwendet.
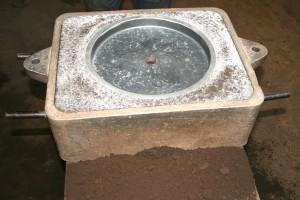
Der gesamte Vorgang lauft auf mehreren Eben ab: Es wird immer wieder Sand nachgefüllt und verdichtet, bis der Unterkasten ein wenig überfüllt und durchweg verdichtet ist. Mit einem Winkeleisen wird dann die Oberfläche sauber abgezogen.
Der Unterkasten wird anschließen herumgedreht, so dass er in der Position des späteren Gusses auf dem Tisch liegt.
Nach dem Aufsetzen und Arretieren des Oberkastens mittels zweier Federbolzen wird das Modell und der ebene Sand im Unterkasten wieder mit Talkumpuder bestäubt. Es werden Formen für den Eingus
s und den Lauf (hinten links) einsetzt und isolierte Röhren als Speiser hineingestellt. Die Speiser werden mit einen Stopfen verschlossen, um das Hineinfallen von Sand zu verhindern. Bei diesem Modell werden bewusst Isoliersteiger verwendet, damit das Metall im Steiger nicht schneller als das Gussteil auskühlt und so ein langes Nachziehen möglich bleibt.
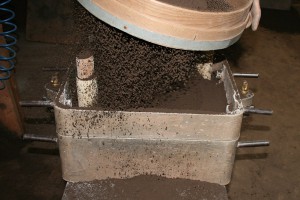
Anschließend wird in den Oberkasten Formsand eingesiebt und wieder wie im Unterkasten mehrschrittig verdichtet und am Ende gerade abgezogen.
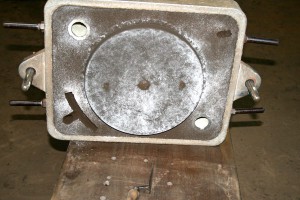
Im nächsten Schritt wird der Oberkasten vorsichtig und möglichst gleichmäßig abgehoben, um ein Ausreißen der Sandform zu
vermeiden. Vorher kann man vorsichtig für leichte Erschütterungen an den Buchsen der Bolzen sorgen, um den Sand etwas vom Modell zu lösen. Nach dem Abheben und dem seitlichen Platzieren wird durch leichtes Klopfen und mit der Lanzette, einer Art Miniatur- Maurerkelle mit Löffelform auf der anderen Seite, das Formobjekt für den Einguss und den Lauf entnommen. Ober- und Unterkasten werden außerdem noch mit Druckluft durch Ausblasen von Sand und Staubresten befreit.
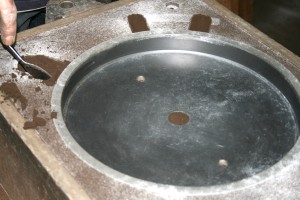
Der Formsand im Unterkasten erhält mit der Lanzette die Ausformungen zum Anschnitt an das spätere Gussteil. Es erfolgt so der „Anschluss“ an den Lauf und die Speiser. Hierbei wird immer wieder vorsichtig geschnitten und der lose Sand möglichst zeitgleich mit Druckluft weggeblasen. Bei sehr großen und tiefen Kästen nutzt man eine Art Staubsauger.
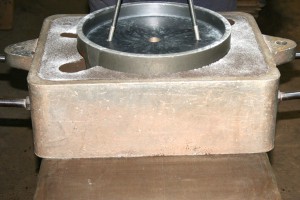
Vor dem eigentlichen Guss wird noch das Modell nach leichtem Klopfen zum Lösen mit zwei langen Augenschrauben vorsichtig nach oben entnommen. Auch hier ist Präzision und eine ruhige Hand gefragt, damit die Sandform nicht beschädigt wird oder Maße verändert werden. Zu dem Zeitpunkt befinden sich noch immer einzelne lose Sandreste im inneren. Um diese zu entfernen, staubt man zunächst vorsichtig ein und bläst anschließend mittels Druckluft aus. Das Einpudern verhindert ein „festblasen“ der losen Partikel in Ecken und Kanten.
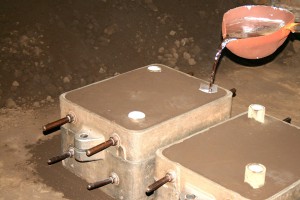
Abschließend erfolgt der Guss: Im Unterschied zum Kokillenguss findet hier eine niedrigwertigere Legierung Verwendung, welche zur Vermeidung von Schaum und Schmutz im Gussteil, der zu Festigkeitsproblemen führen könnte, durch ein Sieb eingegossen wird. Der weitere Gussvorgang ist dem der Kokille ähnlich. Nach kurzer Zeit wird über die Speiser nochmals Aluminium nachgegossen und man kann deutlich ein Nachziehen in das entstehende Gussteil hinein erkennen.
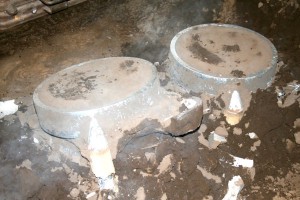
Nachdem man dem Guss einige Minuten zum Erstarren gegeben hat, wird die Sandform zerstört und das Gussteil so entnommen. Es ist dazu oft ausreichend, den Formkasten schwungvoll zu kippen. Die groben Sandreste lassen sich durch kurze, kräftige Hammerschläge auf Einguss oder Speiser beseitigen.
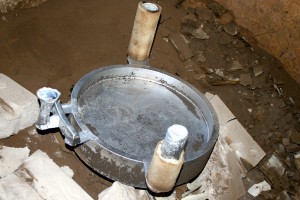
Die Isoliersteiger lassen sich durch das schrumpfende Metall einfach mit leichtem Drehen abziehen und können, sofern sie keinen Schaden genommen haben, für den nächsten Durchlauf wiederverwendet werden.
Nach einigen Stunden der Beobachtung des Form- und Gießprozesses konnte ich selbst aktiv werden und begann mit einer Figur eines Wandbildes. Verglichen mit den anderen Fertigungsverfahren ist hier noch mehr Geduld, Ausdauer und Geschick gefragt, da Fehler beim Abformen in der Regel kaum korrigierbar sind und immer einen kompletten Neuanfang bedeuten. Um die doch recht filigranen Strukturen des Gesichtes der Figur abzuformen, verwendete ich den sogenannten Modellsand. Dabei handelt es sich um den „normalen“, oben erklärten Natursand, mit dem Unterschied, das dieser durch eine große Mühle noch feiner gemahlen wird und vor der Verwendung noch feiner gesiebt wird. Nachdem es bei der Hand der Figur wiederholt zu Abbrüchen kam, wurde hier ein festerer Sand eingesetzt, der außerdem noch Öl enthielt.
Mit diesen Modifikationen war ein problemloses Abformen und Gießen möglich.
Ich konnte außerdem noch zwei Blumentöpfe Abformen und Gießen. Was sich zunächst ziemlich banal anhört, ist doch eine gute Herausforderung wegen dem langen und tiefen Ballen im inneren des Topfes. Das bloße Einstäuben mit Talkumpuder hat in diesem Fall nicht mehr ausgereicht, das Modell wurde daher von innen mit Graphit eingerieben.
Außerdem habe ich mich noch mit dem Abformen und Gießen von Schildern beschäftigt und bei der Produktion von diversen Gussteilen geholfen.
Bei den professionellen Handformern und Gießern hat mich immer wieder das Zusammenspiel der eigentlich im Widerspruch stehenden Aspekte „Kraft“ und „Präzision“ begeistert. Auf der einen Seite ist die Arbeit wirklich körperlich schwer und sehr anstrengend, auf der anderen Seite muss man aber eine extrem ruhige und präzise Hand haben, um alleine die Lanzette ordentlich führen zu können und bei Entnahme des Modell auf gar keinen Fall zu zittern.